Industry Insights and Featured Topics
Here, we provide valuable insights and updates on process safety across industries. Our team of experts curates the latest information, best practices, and emerging trends to empower your organization's safety and compliance efforts. Explore articles, case studies, and webinars, and join the conversation on featured topics shaping the future of process safety. Thank you for choosing us as your resource for staying informed and enhancing safety.
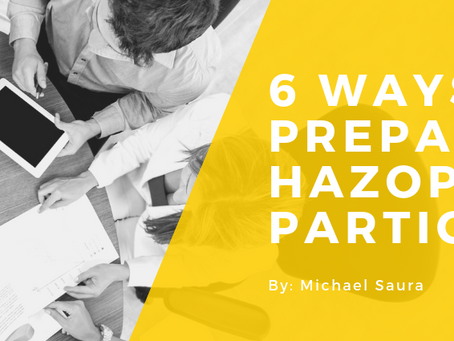
6 Ways You Can Prepare as a HAZOP Participant

This article was originally posted on August 23, 2017 and updated on February 8, 2019. This article can also be found on LinkedIn
You’ve been invited to participate in a HAZOP study. What now?
HAZOP or Hazard and Operability study is a form of analysis used in the chemical processing industry to determine potential hazards and operational issues (gaps), analyze risk for a particular system and make recommendations to reduce intolerable risks. It is a known best practice AND very often, a regulatory requirement such as OSHA Process Safety Management (PSM), EPA Risk Management Plant (RMP), or Control of Major Accident Hazards (COMAH) to name a few.
If you work in an oil refinery, a chemical processing plant, ammonia refrigeration facility or an engineering design firm and you belong to the engineering, maintenance or operations group, there’s a very high probability for you to be invited to participate in a HAZOP that may even dovetail into LOPA.
While an experienced facilitator is necessary so that the study runs smoothly, knowing how and what to prepare as a participant can ensure a high quality study and open up the possibility of finishing ahead of schedule. What’s not to like?
Let’s have a look at 6 ways to prepare for a streamlined study as a participant.
1. Gather Safe Operating Limits (SOL)

Not knowing how far a process parameter can safely deviate can potentially lead to missed hazardous scenarios. On the other hand, I’ve seen scenarios in HAZOP re-validations where the initiating cause resulted in a hazard (overpressure) even if the consequence did not violate any limits (e.g., maximum expected pressure is less than equipment MAWP or maximum allowable working pressure). This can lead to unnecessary or highly conservative recommendations.
Provide the safe upper/lower limit to the facilitator so it can be documented in each node of the study and the team can verify if a consequence for a scenario exceeds these limits. Examples of these could be a process equipment’s MAWP or maximum allowable working temperature (MAWT) and a material’s Nelson Curve limits.
Most likely applies to: Process Engineer, Metallurgical Engineer, Corrosion Specialist, Mechanical Engineer, Operations Representative
2. Brush up on simulation skills

It may have been a while since you have used a simulation program (such as Aspen Hysis), perhaps back in college. It would be good to review the basics since simple simulation can be useful for the HAZOP.
While the HAZOP methodology instructs the team to document the worst credible case for a consequence, not understanding how the system responds to an initiating event can oftentimes lead to overestimation of consequence severity leading to over-designing, which could introduce nuisance trips that are costly and possibly hazardous.
A good example is a loss of reflux case for a tower where the pressure continually rises. In most cases this leads to overpressure of the tower. However, simulation can show an estimate of the maximum potential pressure and overpressure percentage over the MAWP. This allows the team to narrow down whether the consequence is not a hazard or a catastrophic release.
Most likely applies to: Process Engineer
3. Prepare the latest Cause and Effect Diagram & Alarm List

Photo Credit: Siemens
Do you know what your trips do? Do you know what to do if your alarms go off?
The benefits of having this information available are two-fold. First, it allows the team to verify if there is sufficient safeguard response time. Second, when listing safeguards for a scenario, it is best practice to identify what a safeguard’s actions are.
Take for example an instrumented function such as a low fuel gas pressure trip of a gas fired heater. Knowing the trip’s input, set point and action is part of a well-documented HAZOP. Another example is a high-level alarm with specific operator response. The team can verify whether the level alarm being credited provides sufficient time for the operator to diagnose and respond with the appropriate action.
Most likely applies to: Instrumentation Engineer, Process Engineer, Operations Representative
4. Gather Relief Valve Design Basis
When we talk about overpressure scenarios of pressure vessels, the first safeguard that we usually look for are relief valves. Unfortunately, there have been cases where relief valves have been credited as a safeguard only to find out later that it was sized for thermal relief and not for a more demanding overpressure case such as a blocked-in case. The relief valve design basis will help the team understand if the relief valves are sized for such overpressure case and therefore allow the team to decide whether a risk is unmitigated or acceptable.
Most likely applies to: Relief Valve Engineer, Process Engineer
5. Gather Latest Applicable Operating Procedures
Operating Procedures will be referenced from time to time during the HAZOP. Sometimes the only safeguard against certain hazards are well-written and maintained operating procedures (with proper training!). It is best practice to note the procedure number used as safeguards in the study. This also allows the team to verify if the procedures are up-to-date and to truly understand if it can protect against the scenario.
Most likely applies to: Operations Representative
6. Identify Transient Operations
This ties into number 5. Transient operations (such as, manual drains, opening of process equipment, catalyst loading, and gas fired heater cold startup) make about 30% of incidents in the chemical industry. Properly identifying the hazards involved with these types of operations and understanding how the hazard can be prevented is critical. Usually, the HAZOP is a great way to verify this.
Most likely applies to: Operations Representative, Maintenance Representative, Process Engineer
Any favorite tips for increasing productivity and quality in your HAZOP studies? Please comment and share. Also, feel free to subscribe and get updated on my latest blog posts.
#HAZOP #HazardandOperabilityStudy #PHA #ProcessHazardAnalysis #ProcessEngineering #Refining #Refinery #ChemicalProcessing #ProcessSafetyManagement #ProcessSafety #SafetyManagementSystems